GEAR UP FOR SUCCESS: INDUSTRIAL PARTS AND EQUIPMENT INSIGHTS
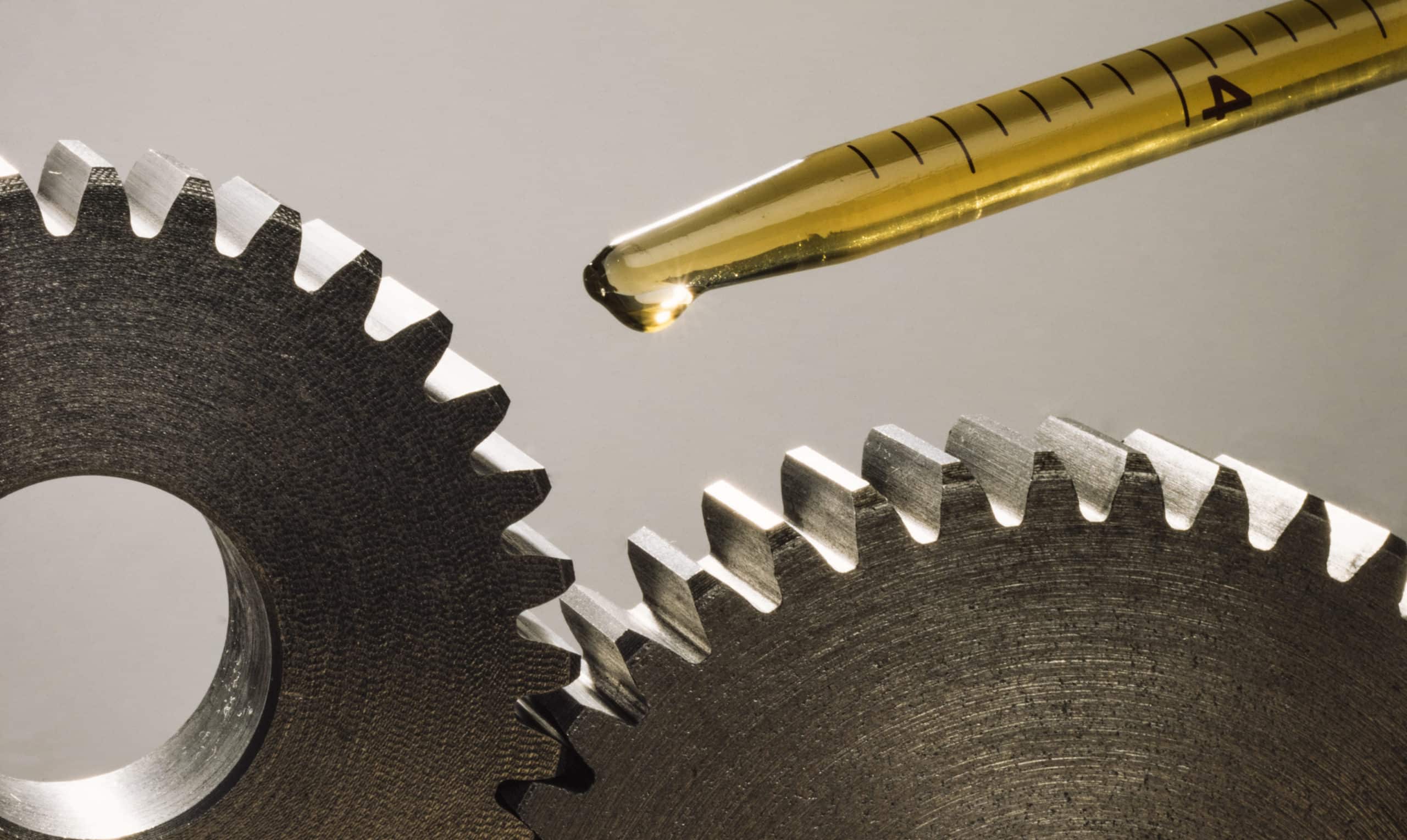
Numerous industrial machinery are essential to manufacturing, mining, construction, rail, aviation, and agricultural projects. However, unnecessary downtime can seriously affect timelines and schedules for the site. Regular planned and preventative care is essential to guarantee both the best possible performance from your capital equipment and the security of its operators. How can you maintain industrial machinery to get the most out of it in terms of production and efficiency? Here are some helpful insights:
Regular inspections are paramount.
Inspections can support you in detecting possible issues, tracking performance, and confirming adherence to rules and guidelines. You should inspect your equipment on a schedule based on the manufacturer’s recommendations, usage frequency, and environmental factors. You should also use a checklist to record the inspection findings and track any necessary repairs or replacements.
Keep extra tools and parts.
You can prevent delays and disturbances in the event of equipment malfunction or damage by keeping spare parts and tools on hand. High-quality tools and spare parts from Kor Pak will enable you to complete repairs or replacements quickly and effectively. It is advisable to maintain a record of the necessary tools and spare parts for your equipment and to restock them as needed. Along with clearly labeling them, you should keep them in a safe place that is also easily accessible.
Observe preventive maintenance.
The practice of carrying out regular maintenance to keep equipment from breaking down and increasing its lifespan is known as preventive maintenance. Performing cleaning, lubricating, adjusting, calibrating, and part replacements are examples of preventive maintenance. Preventive maintenance plans that specify the duties, intervals, and accountability for each piece of equipment are important to adhere to. You should also employ methods and instruments to maximize your preventive maintenance plan, including reliability-centered maintenance, condition monitoring, and predictive maintenance.
Diagnose and fix common problems.
Even with routine maintenance, industrial equipment might still have problems that impair its efficiency and productivity. You can identify and fix common issues before they worsen or do more harm by troubleshooting them. Learn about the typical problems with your equipment, like leaks, noises, vibrations, overheating, or malfunctions. Additionally, you ought to adhere to the instructions and troubleshooting techniques provided by the maker or a certified specialist.
Train your staff
Another essential component of equipment maintenance is teaching your employees how to use, operate, and maintain your equipment. You can ensure that your operators follow the proper procedures, don’t make mistakes, and report any problems by providing them with training. Your employees should receive frequent, up-to-date training on the equipment’s features, operations, safety, and maintenance. Encourage your employees to provide management and one another with comments, ideas, and best practices.
Seek expert assistance.
Equipment problems can occasionally be outside your competence and necessitate expert assistance. Hiring a professional ensures that a skilled and knowledgeable technician fixes or maintains your equipment. You should seek specialist assistance when faced with challenging, persistent, or dangerous problems you cannot handle alone. You should also get professional help regarding large equipment overhauls, upgrades, or adjustments.
Conclusion
The above insights will help you care for and maintain your industrial machinery.